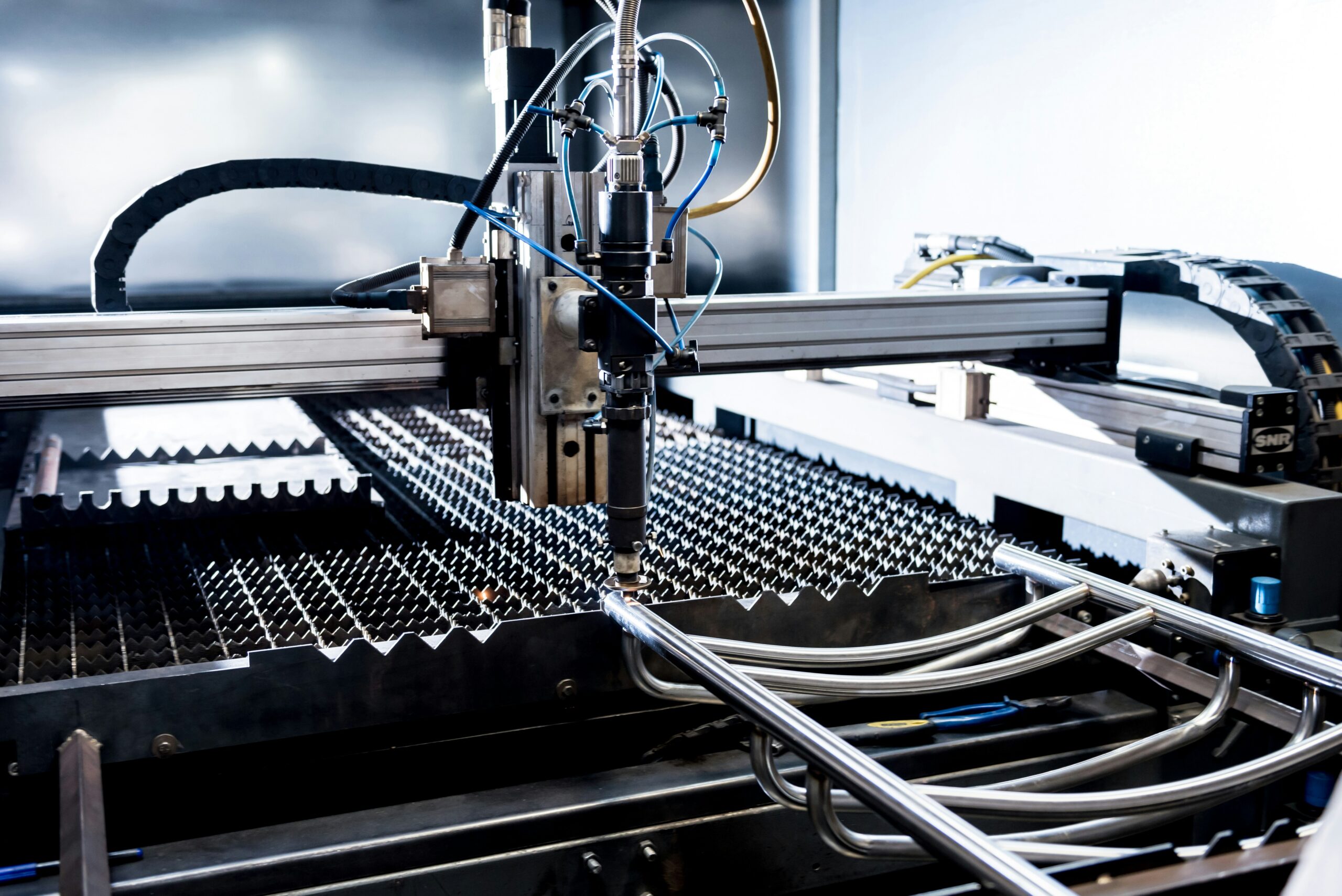
In the ever-evolving landscape of manufacturing, success hinges on more than just innovation and technology. Behind every efficient assembly line, quality product, and sustainable operation lies an often-underappreciated factor: process design. This crucial component shapes the backbone of modern manufacturing, optimizing resources, improving quality, and fostering adaptability in a rapidly changing industrial world.
Understanding Process Design in Manufacturing
Process design refers to the strategic planning and organization of manufacturing methods to achieve specific objectives. It involves determining the sequence of operations, selecting appropriate machinery, and allocating resources efficiently to ensure optimal production outcomes. Process design is not just about producing goods; it’s about creating value through precision, efficiency, and cost-effectiveness.
Modern manufacturing demands processes that are streamlined, scalable, and resilient. Companies must integrate process design into their operational frameworks to ensure competitiveness in a market defined by constant innovation and customer demand for high-quality products.
Efficiency as the Cornerstone
One of the primary goals of process design is to enhance efficiency. Time, labor, and materials are precious resources that must be utilized judiciously. By carefully planning workflows, manufacturers can minimize waste, reduce production time, and maximize output without compromising quality.
For example, adopting lean manufacturing principles, which focus on eliminating non-value-adding activities, relies heavily on effective process design. When processes are thoughtfully designed, bottlenecks are avoided, and production lines operate smoothly. This reduces costs and boosts productivity, allowing businesses to deliver products faster and at competitive prices.
Quality Enhancement Through Structured Processes
Another vital aspect of process design is its impact on product quality. In modern manufacturing, consistency is key to building customer trust and loyalty. A well-designed process ensures that each product meets the same high standards, minimizing defects and variations.
Process design incorporates quality control measures at every stage of production. From automated inspections to real-time monitoring systems, manufacturers can catch errors early and prevent defective products from reaching customers. This proactive approach saves recalls or warranty claims costs and upholds a company’s reputation in a competitive marketplace.
Sustainability in Manufacturing
The global emphasis on environmental sustainability has transformed how manufacturers approach process design. Today, businesses are expected to reduce their environmental footprint while maintaining profitability. Process design is pivotal in achieving this balance by optimizing energy use, reducing waste, and incorporating sustainable materials.
For instance, manufacturers are increasingly adopting circular economy principles, where waste materials are recycled back into production cycles. This requires reevaluating traditional manufacturing processes to integrate recycling and reusability seamlessly. Thoughtful process design enables manufacturers to align with global sustainability goals while meeting customer expectations for eco-friendly products.
The Role of Technology in Process Design
Technology has become a game-changer in process design. Advanced tools such as computer-aided design (CAD), computer-aided manufacturing (CAM), and simulation software allow manufacturers to visualize and test processes before implementation. These tools help identify inefficiencies and potential issues, enabling corrections without costly trial-and-error methods on the shop floor.
The rise of Industry 4.0 technologies, such as the Internet of Things (IoT), artificial intelligence (AI), and robotics, has revolutionized process design. Smart sensors provide real-time data on machine performance and production metrics, while AI algorithms analyze this data to suggest improvements. Robots handle repetitive tasks precisely, freeing human workers for more complex activities.
These technologies enhance efficiency and provide flexibility. Manufacturers can adapt processes quickly to accommodate changes in demand or shifts in product design, ensuring they remain agile in an increasingly dynamic market.
Meeting Customer Expectations
In today’s consumer-driven world, customers demand customized products, shorter delivery times, and impeccable quality. Process design enables manufacturers to meet these expectations while maintaining profitability. By streamlining workflows and incorporating modular production methods, companies can produce various products without extensive downtime or retooling.
For example, mass customization—a trend where consumers can personalize products to their liking—relies heavily on adaptable process design. Modular manufacturing setups allow for quick changes between product configurations, allowing customers to choose options that suit their preferences.
The Human Element in Process Design
While technology plays a significant role in modern manufacturing, the human element remains indispensable. Workers bring creativity, problem-solving skills, and adaptability to the production floor—qualities machines cannot replicate. Process design must consider the needs and capabilities of employees to ensure their well-being and productivity.
Ergonomics is a critical aspect of process design. Manufacturers can enhance employee satisfaction and reduce the risk of injuries by designing workstations and workflows that reduce physical strain. Additionally, involving workers in the process design phase fosters a sense of ownership and encourages innovative ideas for improvement.
Challenges and Opportunities
Despite its benefits, process design in modern manufacturing is not without challenges. Rapid technological advancements, fluctuating market demands, and supply chain disruptions require constant adaptation. Manufacturers must strike a balance between maintaining operational stability and embracing change.
However, these challenges also present growth opportunities. Companies that invest in continuous improvement and stay ahead of trends can gain a competitive edge. Collaboration between departments, ongoing employee training, and partnerships with technology providers can help manufacturers overcome obstacles and thrive.
The Future of Process Design
As manufacturing evolves, process design will play an even more significant role in shaping its future. Emerging trends such as additive manufacturing (3D printing), green manufacturing, and digital twins—virtual models of physical systems—promise to redefine what’s possible.
To remain competitive, manufacturers must prioritize innovation in process design, embracing technologies and strategies that drive efficiency, quality, and sustainability. By doing so, they can ensure long-term success in a world where adaptability is the key to survival.
The importance of process design in modern manufacturing cannot be overstated. It is the foundation upon which efficiency, quality, sustainability, and customer satisfaction are built. As the industry continues to advance, investing in thoughtful and innovative process design will remain essential for manufacturers seeking to stay ahead in a competitive and ever-changing market. By prioritizing this critical element, companies can transform challenges into opportunities and achieve enduring success.